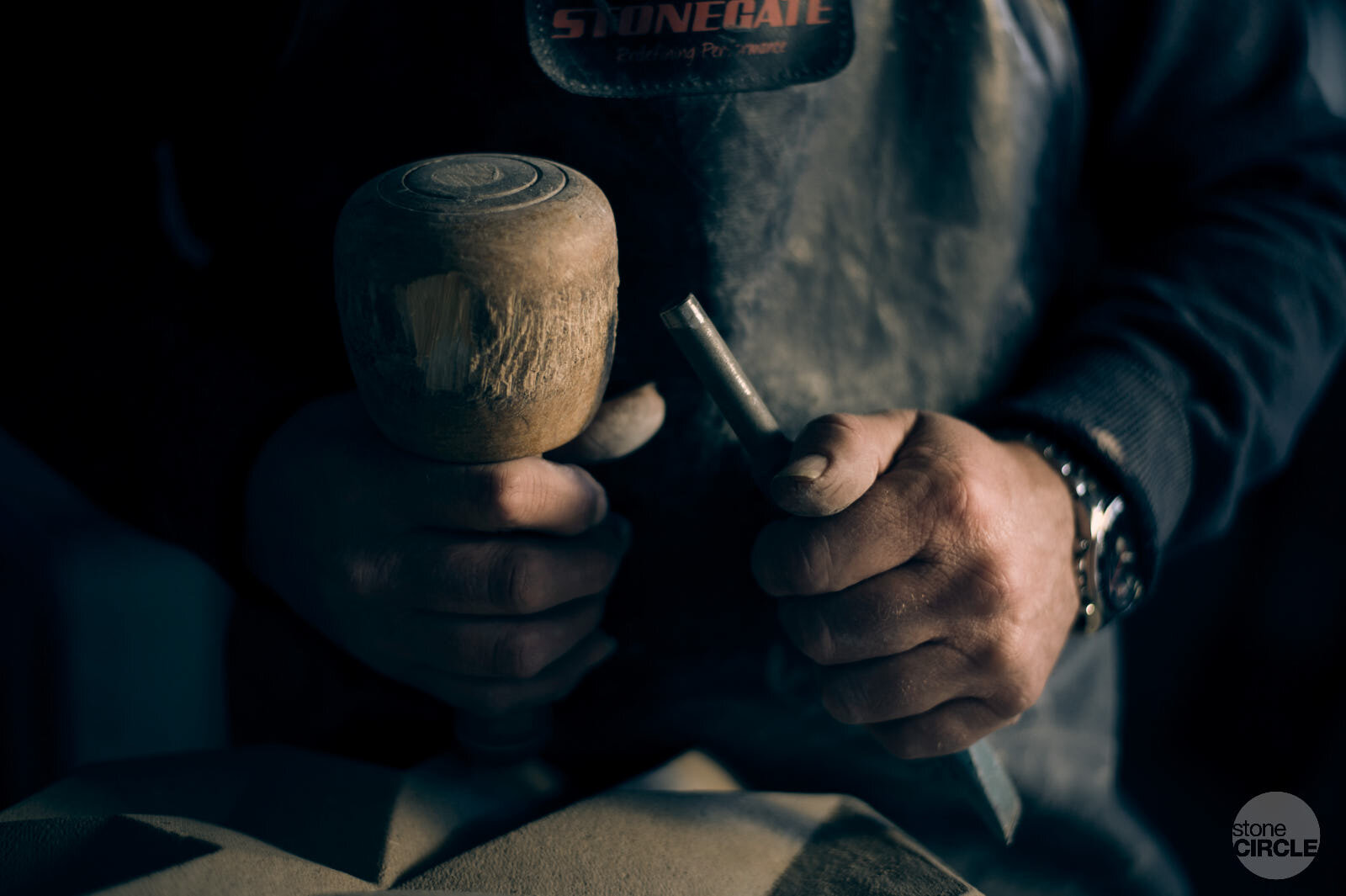
a blend of old and new
perhaps unique to our industry is the fact that the stone working technology has not supplanted the hand skills which are still as important as ever
What has changed dramatically over the years is the type of machinery used in this age-old sequence. Perhaps unique to our industry, however, is the fact that the stone working technology has not supplanted the hand skills which are still as important as ever. The majority of our machines are computer numerically controlled (CNC), and these enable great accuracy when used in conjunction with computer-aided design and digital templating. They have improved productivity by doing the often laborious task of removing large amounts of stone, leaving the masons to carry out the final finishing and quality control by hand. This has also led to a safer environment for the masons with much less dust being generated. With our gantry and pillar cranes equipped with vacuum lifting devices, there is now much less lifting and handling.
The sequence of events which brings natural stone from the quarry to the home has not changed much since stone entered the homes of our ancestors. Large blocks of stone are cut from the quarry. From those blocks, thin pieces of stone are cut called slabs which are usually polished on one face.
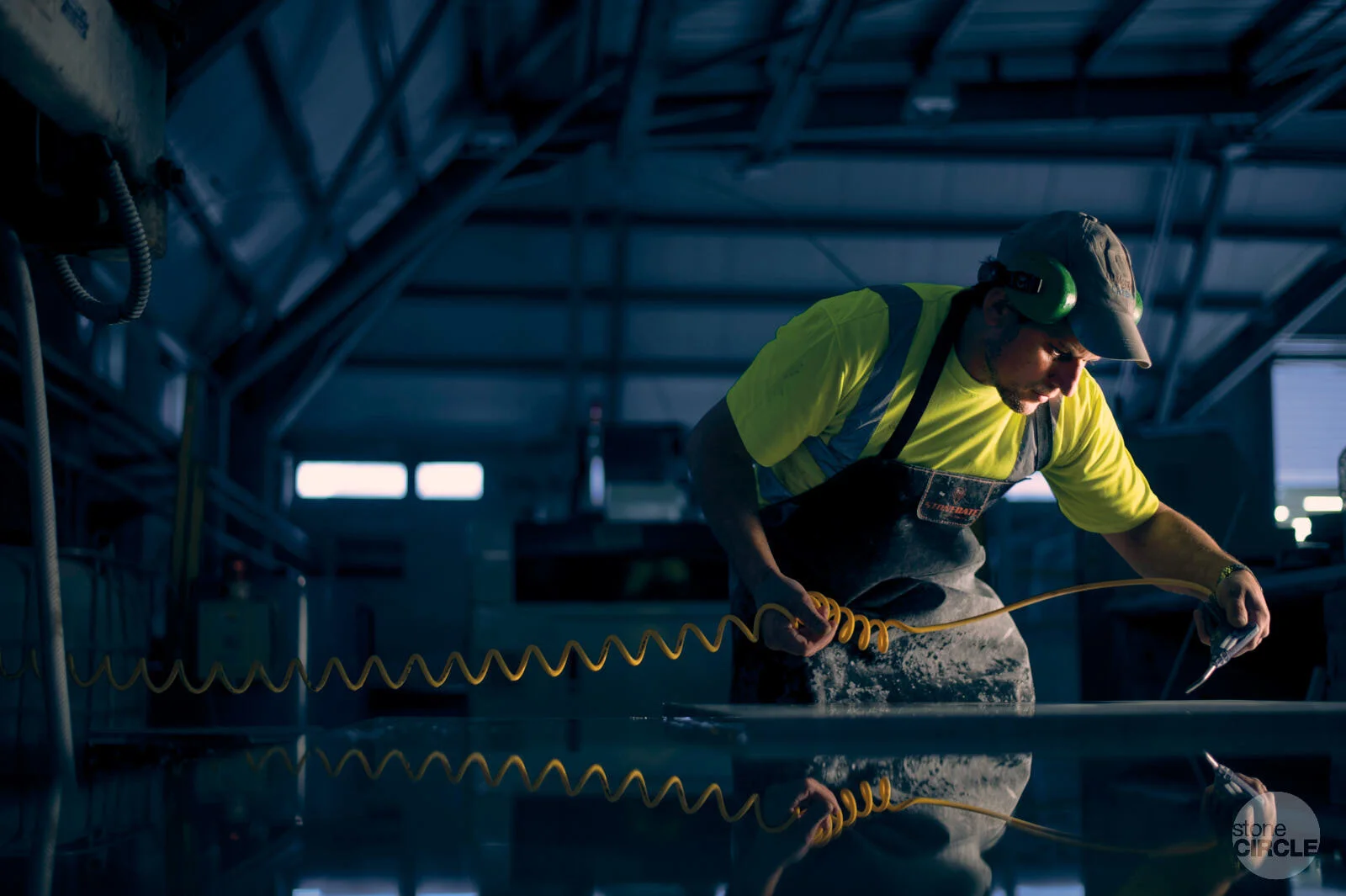

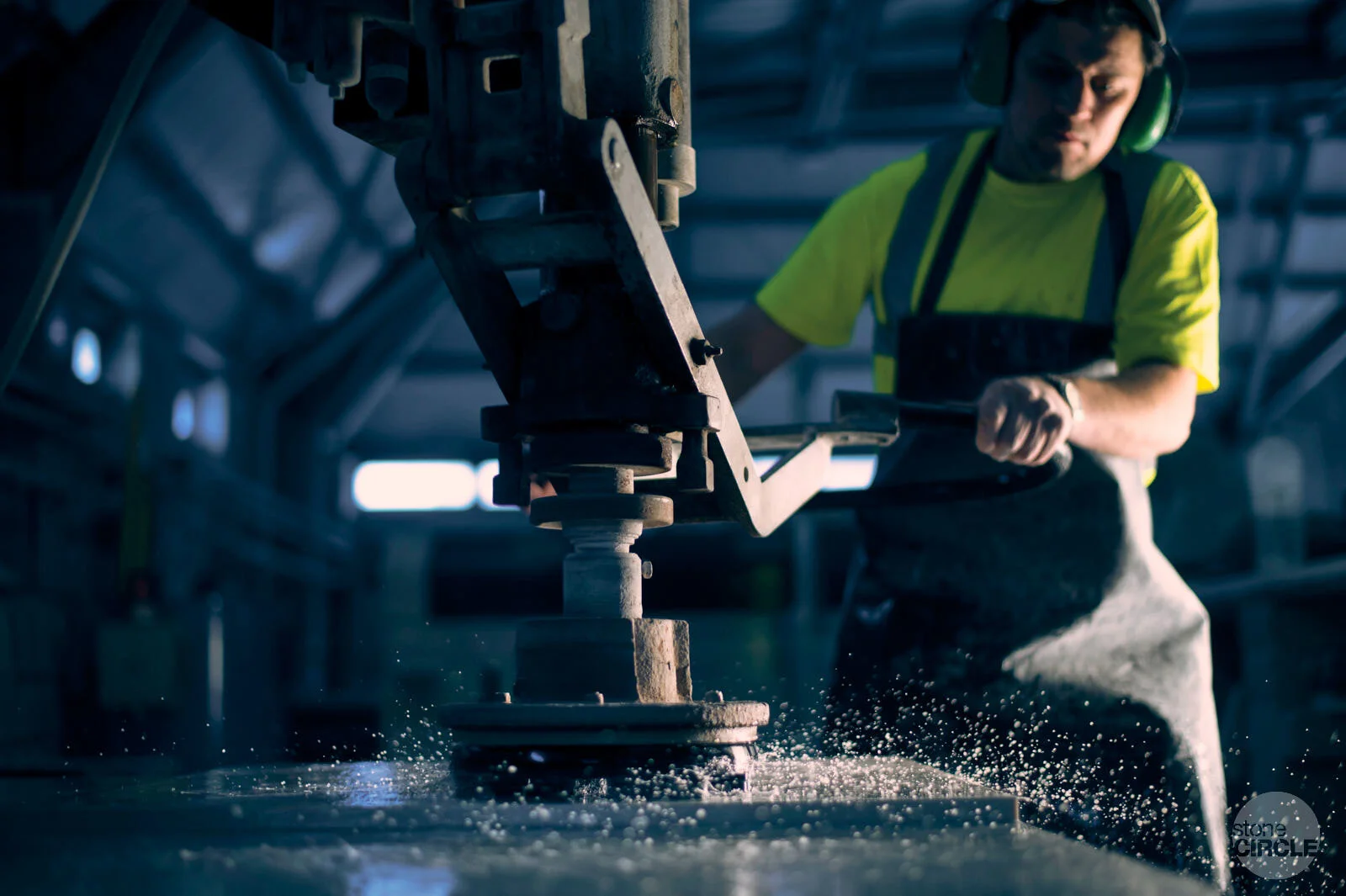
Nowadays we free from the ‘hard graft’ experienced by previous generations of stonemasons. That allows the artistic talents, creativity and skill of our modern-day masons to develop and find expression in the stonework we produce.
technology with a human touch
As with everything else, the final inspection for quality and conformity still requires a human touch.
‘If it is not broke, don’t fix it’ is entirely true. But even though our modern machinery and techniques have improved what we can do, we still use a simple polishing machine that has changed little in 60 years. As an example of the synergies between processes, we make surfaces from the most delicate white onyx that are installed into a modern passenger jetliner. The onyx is bonded to lightweight honeycomb under vacuum to remove the air from the glue. The honeycomb adds strength to the stone, allowing us to mill the thickness down from 20mm to 10mm – all to reduce the weight. We then apply a fine-honed surface finish using our 40-year-old polishing machine before the final shape is cut on the waterjet machine. This machine produces a 60000psi jet of water mixed with a fine abrasive garnet which is CNC driven to cut out the shape required with perfect accuracy.